Peerless Info About Can We Run Delta Motor In Star
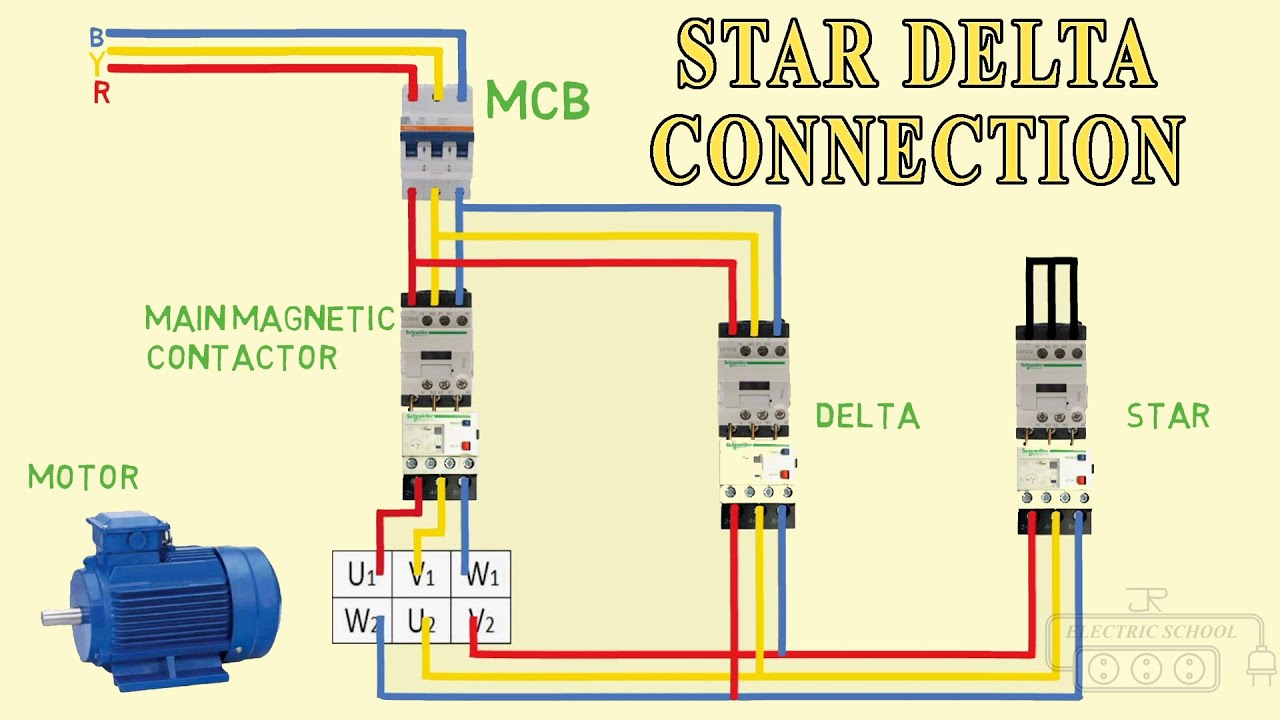
Why Motor Connected In Star Delta
Understanding the Star-Delta Starter
1. Why Star-Delta? Avoiding a Motor Meltdown
So, you're pondering the question: can a delta-connected motor actually run in a star configuration? The short, slightly unsatisfying answer is: sometimes. Let's unpack that. Think of starting a big induction motor like trying to sprint from a dead stop in fifth gear. It requires a massive surge of current, often 5-7 times the normal running current. This "inrush current" can wreak havoc on your electrical system, causing voltage dips, tripping breakers, and generally stressing everything out. The star-delta starter is a clever solution to this problem.
Imagine the star configuration as a temporary training wheel. By initially connecting the motor windings in a star (Y) configuration, we effectively reduce the voltage applied to each winding. Remember that in a star connection, the line voltage is 3 (approximately 1.732) times the phase voltage. So, we're giving the motor a "soft start," limiting that pesky inrush current and preventing a mini-electrical apocalypse. Think of it like easing into that sprint in first gear before shifting up.
Once the motor reaches a certain speed (typically around 70-80% of its full speed), a timer switches the connection to a delta configuration. Now, the motor receives the full rated voltage, allowing it to deliver its full torque and power. It's like finally hitting fifth gear and cruising along at full speed. The transition needs to be relatively smooth to avoid a second, smaller current surge, but the initial impact is significantly reduced. It's all about damage control, really.
So, to reiterate, the star-delta starter isn't about permanently running a delta motor in star. It's about starting it in star to mitigate the initial current surge. It's a temporary measure, a helping hand to get the motor going without blowing all the fuses. Think of it as a carefully choreographed dance between voltage and current, all in the name of a happy, healthy motor and electrical system.
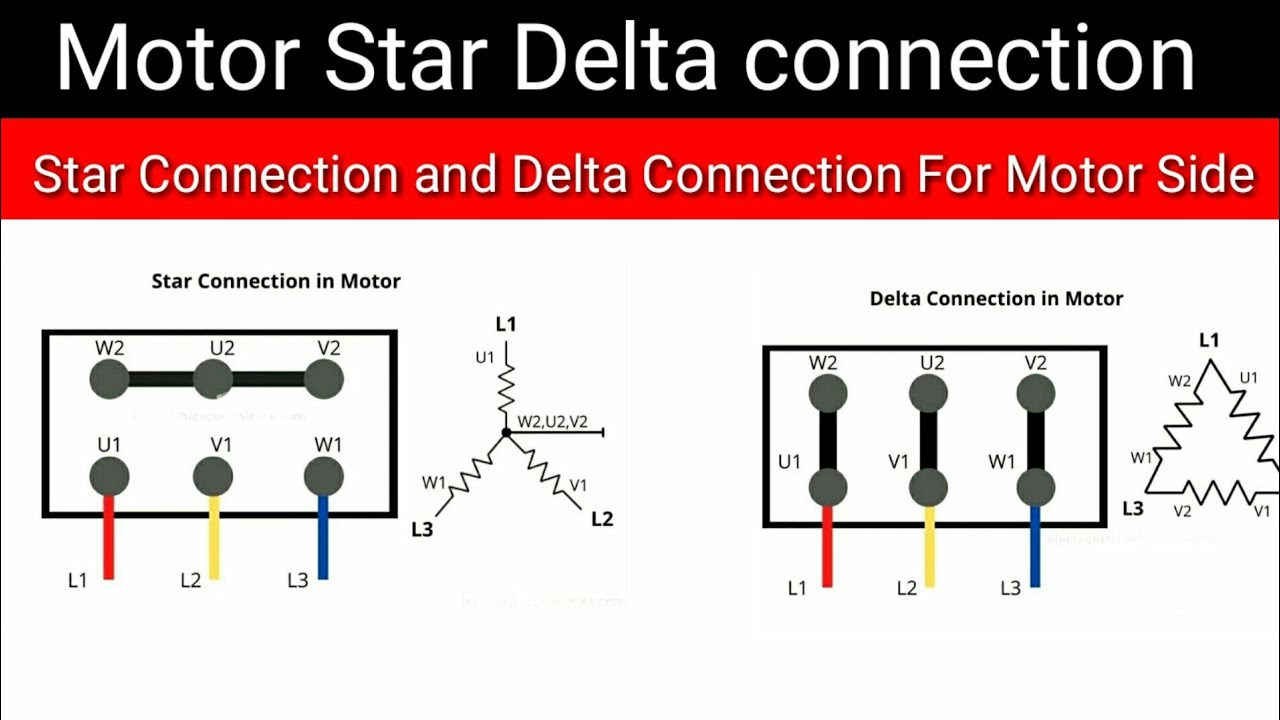
The Nitty-Gritty
2. Horsepower and Application Scenarios
Now, let's delve a bit deeper into the "when" and "why" of star-delta starters. They're not a universal solution for every motor. Typically, they're employed for larger induction motors, often those above 5 horsepower (though the exact threshold can vary depending on the specific electrical system and local regulations). Smaller motors often don't generate enough inrush current to warrant the complexity and cost of a star-delta starter.
Think of applications like pumps, fans, compressors, and conveyors — equipment that requires significant starting torque and can benefit from a reduced voltage start. In these scenarios, the star-delta starter helps protect the motor, the electrical infrastructure, and other connected equipment from the stresses of high inrush currents. For example, a large water pump starting directly online could cause a significant voltage drop, potentially affecting other sensitive equipment connected to the same power source. A star-delta starter mitigates this risk.
But it's not just about protection. Star-delta starters can also extend the lifespan of the motor itself. By reducing the thermal stress associated with high inrush currents, they can help prevent premature insulation breakdown and winding damage. It's like giving your car a gentler start; it's bound to last longer. Furthermore, some power companies may incentivize or even mandate the use of reduced voltage starters for larger motors to minimize the impact on the overall grid.
However, there are limitations. Star-delta starting reduces the starting torque to about one-third of the direct-on-line (DOL) starting torque. This means it's not suitable for applications that require high starting torque, such as heavily loaded conveyors or equipment that needs to overcome significant static friction. In these cases, alternative starting methods, like auto-transformers or soft starters, might be more appropriate. It's all about matching the starting method to the specific application requirements.

Star Delta Connection In Motor Terminal Block
Star vs. Delta
3. Voltage, Current, and Configuration Considerations
Okay, let's quickly revisit the core difference between star and delta connections, electrically speaking. In a star (Y) connection, the three windings are connected together at a common point (the neutral), forming a "Y" shape. The voltage across each winding (the phase voltage) is lower than the voltage between the lines (the line voltage). As mentioned earlier, the line voltage is 3 times the phase voltage.
In contrast, in a delta (Δ) connection, the windings are connected in a closed loop, forming a triangle. In this configuration, the line voltage and the phase voltage are equal. However, the line current is 3 times the phase current. It's a bit like two sides of the same coin; one emphasizes voltage reduction, while the other maintains full voltage but distributes current differently.
The key takeaway here is that the star configuration provides a lower voltage across the motor windings during the starting phase, reducing the inrush current. The delta configuration, on the other hand, delivers the full rated voltage for normal operation. Understanding these fundamental differences is crucial for grasping the purpose and function of a star-delta starter. It's like knowing the difference between a low gear for climbing hills and a high gear for cruising on the highway.
Furthermore, the motor itself must be designed to operate in delta configuration at the supply voltage. This means that the nameplate voltage of the motor should match the line voltage of the power supply when connected in delta. If the motor is not designed for delta operation at the supply voltage, running it in delta would likely result in overheating and damage. So, always double-check the motor's nameplate information before implementing a star-delta starter.
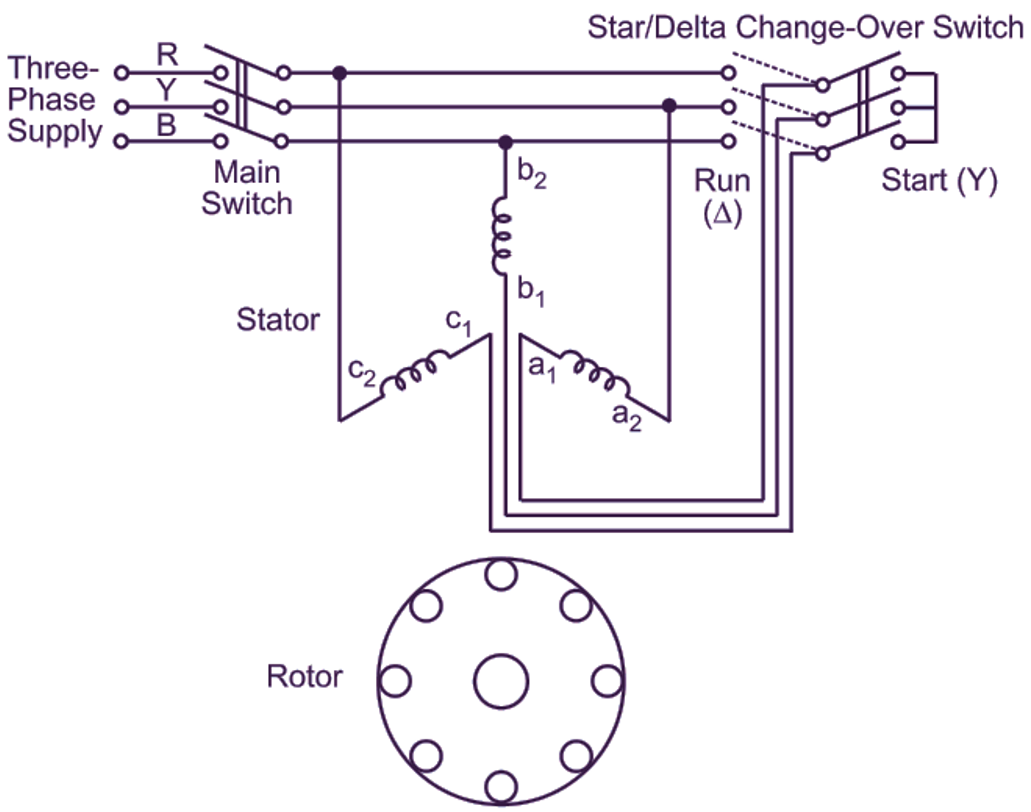
What Is Star Delta Starter? Working & Diagram ElectricalWorkbook
Potential Pitfalls
4. Torque, Transition, and Thermal Overload
While star-delta starters are a useful tool, they're not without their potential pitfalls. One of the most common mistakes is using them in applications where the starting torque requirement is too high. Remember that the star connection reduces the starting torque significantly. If the motor can't overcome the load's inertia in the star configuration, it will stall, and the starter will likely trip out on overload. This can be a frustrating and potentially damaging situation.
Another critical aspect is the transition from star to delta. The timing of this transition is crucial. If it happens too early, the motor won't have reached sufficient speed, and the current surge will still be significant. If it happens too late, the motor will be operating in the star configuration for longer than necessary, limiting its torque output. The ideal transition point is typically around 70-80% of the motor's rated speed, but this may need to be adjusted based on the specific application.
Proper overload protection is also essential. Even with a star-delta starter, the motor can still be subjected to overloads, especially during the transition phase. Ensure that the overload relay is properly sized and configured to protect the motor from excessive current draw. A thermal overload relay is your friend; it's the motor's last line of defense against overheating and damage. Don't skimp on it.
Finally, consider the thermal implications. Starting a motor, even with a reduced voltage starter, generates heat. Repeated starts and stops can cause the motor to overheat, shortening its lifespan. If the application requires frequent starting and stopping, consider using a soft starter, which provides a smoother and more controlled start, reducing thermal stress on the motor. It's all about finding the right balance between performance and longevity.
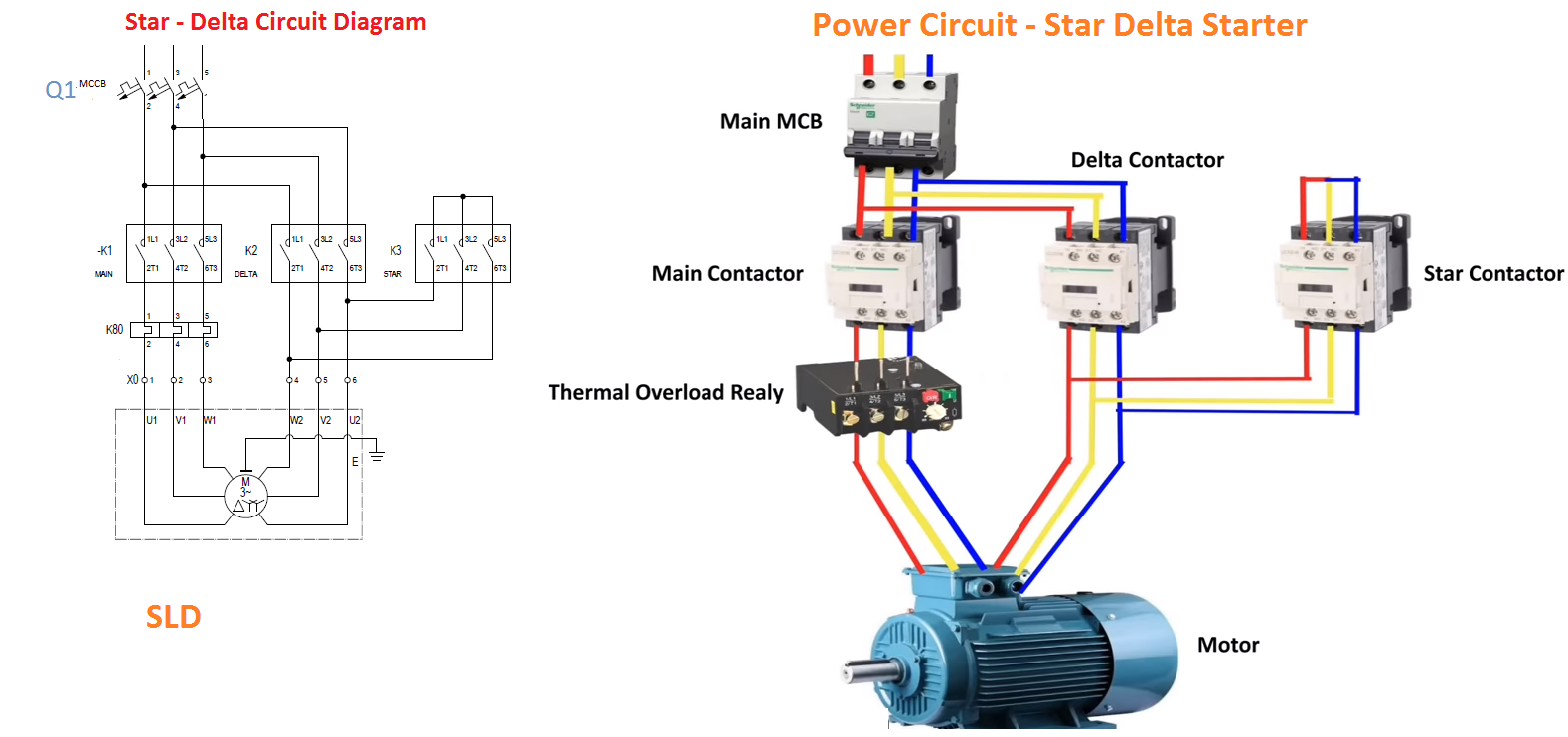
Star Delta Motor Connection Circuit Diagram
Beyond Star-Delta
5. Soft Starters and Variable Frequency Drives (VFDs)
While star-delta starters are a common solution, they're not the only game in town. Other reduced voltage starting methods, such as auto-transformers and soft starters, offer different advantages and disadvantages. Auto-transformers provide a more controlled voltage reduction than star-delta starters, but they are also more expensive and complex.
Soft starters, on the other hand, use solid-state devices (thyristors or silicon-controlled rectifiers) to gradually increase the voltage applied to the motor, providing a smoother and more controlled start than star-delta starters. They offer adjustable starting parameters, such as starting voltage and ramp-up time, allowing for fine-tuning of the starting characteristics to match the specific application requirements. Soft starters are generally more expensive than star-delta starters, but they offer superior performance and protection.
And then there are Variable Frequency Drives (VFDs). VFDs offer the ultimate in motor control. They not only control the voltage but also the frequency applied to the motor, allowing for precise control of speed and torque. VFDs provide the smoothest possible start, eliminating inrush current altogether. They also offer energy savings by allowing the motor to operate at reduced speeds when full output is not required. However, VFDs are the most expensive and complex of all motor starting methods.
The choice of starting method depends on a variety of factors, including the size of the motor, the starting torque requirements, the frequency of starts and stops, the sensitivity of the connected equipment, and the available budget. Each method has its strengths and weaknesses, and the best solution is the one that best meets the specific needs of the application. It's like choosing the right tool for the job; a hammer might be great for driving nails, but it's not the best choice for tightening screws.

3 Phase Star Delta Motor Connection Diagram » Wiring Work
FAQs
6. Addressing Common Questions and Concerns
Let's tackle some frequently asked questions about star-delta starters to clarify any remaining confusion.
Q: Can I use a star-delta starter on any motor?
A: No, not every motor is suitable. The motor must be designed for delta operation at the supply voltage. Check the motor's nameplate for this information. If the motor is not designed for delta operation, using a star-delta starter can damage it.
Q: What happens if the motor stalls during the star start?
A: If the motor stalls in the star configuration, it indicates that the starting torque is insufficient to overcome the load's inertia. The starter will likely trip out on overload. You may need to consider a different starting method or reduce the load during start-up.
Q: Is a soft starter always better than a star-delta starter?
A: Not necessarily. Soft starters offer superior performance and protection, but they are also more expensive. If the application doesn't require the advanced features of a soft starter and the budget is a concern, a star-delta starter may be a perfectly acceptable solution.
Q: Can I convert a DOL starter to a star-delta starter?
A: Technically, yes, but it's generally not recommended. Converting a DOL starter to a star-delta starter involves significant rewiring and component changes. It's often more cost-effective and reliable to purchase a pre-built star-delta starter.
Q: How do I troubleshoot a star-delta starter that's not working?
A: Troubleshooting a star-delta starter requires a systematic approach. Check the wiring connections, the timer settings, the overload relay, and the motor windings. Use a multimeter to check for voltage and continuity. If you're not comfortable working with electrical equipment, consult a qualified electrician.